CYPET: The family-run business that has set out to revolutionise the PET industry with its innovative machines
Adonis Adoni 07:00 - 12 January 2025
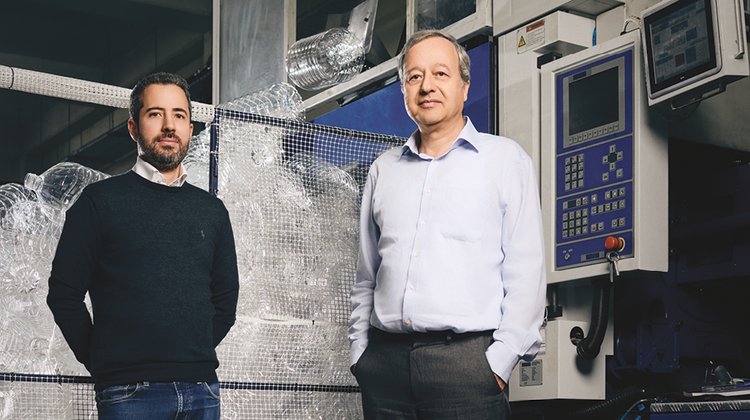
Constantinos and Michalis Sideris, respectively the Director/General Manager and Head of Business Operations for CYPET Technologies, discuss their plans to revolutionise the PET industry and the challenges of launching a manufacturing business with a global appetite from Cyprus.
Inside the CYPET Technologies conference room, a wall-to-wall shelf is laden with PET containers of almost every conceivable size. There are tiny 20-millilitre bottles, 10-litre water containers, jerrycans, drums big enough to be used as makeshift bar tables and everything in between. All are made of polyethylene terephthalate (PET), the most recyclable and recycled plastic in the European Union. “Our machines are the only ones capable of producing PET containers bigger than 20 litres. We’ve actually sold machines for 50, 60 and 120-litre containers,” explains Director/General Manager Constantinos Sideris with evident pride.
Having lived and breathed plastics for decades, holding various managerial roles in the industry, Constantinos Sideris took the helm of the family business M. Sideris & Sons at the turn of the millennium. The three-decades-old company then operated as a trader, dealing in plastics, machinery and materials. Determined to breathe new life into the business, Sideris set a bold course in 2005 to design and build novel machines for manufacturing PET bottles and containers. The ambitious pivot was no small feat and, as he would soon learn, developing an engineering and design infrastructure to support this vision was just one of many roadblocks along the way.
On the ground floor of CYPET’s facility in the sprawl of the Dali industrial zone, the company’s first-generation injection stretch blow moulding (ISBN) machine hums steadily, coaxing raw PET into sleek 10-litre water containers. These emerge with metronomic precision, dropping into a towering mesh box that fills up in about 45 minutes. Next to it stands the newer model: slicker, sleeker and smaller, like a younger sibling outshining the eldest. Nearby, a forklift operator manoeuvres pallets of materials with practiced nonchalance, while across the floor, a workshop is busy with the relaxed chaos of creativity. Stacks of boxes marked with origins from around the globe line the walls. “These are machine parts,” says Constantinos’ son Michalis Sideris, the company’s Head of Business Operations, explaining that CYPET designs the parts and moulds in Cyprus, has them manufactured abroad and does the full assembly locally, performing rigorous tests before shipping them out.
From Formula 1 to a small family-run business
For the third generation of the family business, Michalis Sideris' path to the industry was a bit more cinematic. From a young age, he wanted to break into Formula 1 and so he earned a mechanical engineering degree from the University of Cambridge – his father’s alma mater – before venturing into various internships that landed him with McLaren Racing around 2011. There, he worked for five years in vehicle dynamics, helping develop mathematical models to predict how cars would perform on the track. It was a high-pressure, high-performance environment that shaped his understanding of teamwork, problem-solving and innovation. Now, he says, “I’m trying to instil those same values and methodologies into the CYPET team.”
CYPET has well-developed design and engineering departments – of the company’s 24 employees, 18 are engineers – handling everything from mechanical and pneumatic systems to automation and software development. It also has a 12-strong team stationed in India, which represents the lion's share of its revenues, acting as the local factory. So how did he go from jet-setting with the McLaren F1 team to the humbler confines of a family-run business at the eastern end of the Mediterranean? Michalis Sideris offers a simple answer. “I wanted to start a family.” With his then fiancée – now wife – also a Cypriot, coming back home and continuing the Sideris legacy seemed like the most obvious choice.
The struggle to get funding and become known
The Cypriot investment landscape has never been fertile ground for high-ticket items. It is a place where big ideas, like CYPET’s multi-million-euro machines, become reality with a huge amount of caution. Back in the conference room, Constantinos Sideris, measured but unsparing, passes the following verdict, “The innovation ecosystem in Cyprus has improved a lot but the funding infrastructure is still not there.” Even as Cyprus carves out a niche in the burgeoning video games market that occasionally draws Series A rounds, the local investment scene remains fixated on early-stage ventures.
Indeed, this is the strategy of the Cyprus Equity Fund, operated by 33East, and armed with a modest €37.5 million from Cyprus’ Recovery and Resilience Facility and leftovers from the JEREMIE programme. To commercialise its first machine, CYPET had to cast its net farther afield, pulling funds from abroad. In 2013, the company spun out from its legacy business, becoming an independent entity with all the risks and rewards that entailed. But pitching a novel machine, costing several hundred thousand euros and made by an unknown company in a country some wouldn’t even find on the map, was no mean feat. “You needed to build trust,” Michalis Sideris says. “If a potential customer doesn’t know who you are and hasn’t heard of your company before – these are red flags.”
The early years were a hard slog: one or two machines sold annually, with CYPET’s clientele strictly the brave and the needy: early adopters or firms pressed for containers that only their machines could conjure. The gale force of the coronavirus pandemic compounded the issue by freezing the investment pipelines, as customers sewed their wallets shut. But the company has weathered the storm: today, CYPET sells six to eight machines annually across 19 countries, each unit priced between €400,000 and €500,000. Its patents tween €400,000 and €500,000. Its machines have proven particularly competitive in the 5-to-20 litre range, mainly water bottles and edible oil containers. And looking forward, father and son now see only clear skies ahead.
What is PET?
Polyethylene terephthalate (PET) was first synthesised in the early 1940s, with chemical company DuPont in North America developing it for textile fibres by the mid-1940s. PET’s breakthrough in bottle manufacturing came in the 1970s when the first PET bottles were patented, marking a revolution in packaging. Lightweight, sturdy, PET is food-safe, resistant to microorganisms and chemicals, and has excellent wear characteristics. In 2022, Europe utilised 5 million tonnes of PET in packaging and of this, 3 million tonnes were collected, achieving a 60% rate. Beverage bottles represented the majority, with a 75% recycling rate, a benchmark other plastics struggle to match. Globally, the PET market is expected to grow to US$43.26 billion by 2029.
While there are ongoing discussions among manufacturers like Japan’s brewing and distilling company Suntory to switch to 100% sustainable bottles, Constantinos Sideris clarifies: “That likely means switching from fossil-based PET to plant-based plastics, such as plant-based PET or PLA, both of which can be processed on CYPET’s machines. PET is the most sustainable plastic material because it’s the only one that can be recycled as many times as you want by upgrading it to its original properties.” He adds that a recent lifecycle analysis found that PET generates about half the greenhouse gas emissions of other plastics. Recently, a major beverage brand (its identity carefully under wraps) has enlisted CYPET to develop PET packaging to replace its existing polyethylene options. “We see a growing shift from other plastics to PET because of its sustainability benefits. Sustainability is an opportunity, not a threat,” says the Director/General Manager, underscoring CYPET’s position to ride the industry trend.
Machine capable of producing 1000-litre tanks set to revolutionise the industry
To fortify itself against the next investment climate upheaval, the company has undertaken two actions. The first was to develop a machine capable of producing 1000-litre tanks. The duo believes it will revolutionise the industry, naturally creating substantial growth potential for the company, as a PET container weighs about half its polyethylene counterpart, translating into environmental and financial savings. CYPET has already secured a customer in Asia and the first machine is already built, waiting for the moulds to arrive to begin testing, with market entry slated for Q1 2025.
The second is a machine targeting 20ml-5L bottles, which is the largest segment of the PET market. This machine is up to 3 times more productive (in terms of bottles per hour) compared to existing CYPET machines, making it very competitive against other machines on the market. The company is already discussing the building of the prototype with investors, with commercialisation scheduled for Q4 2025.
“We’re still a very small company globally but, hopefully, these new product launches will kick off a very steep growth trajectory,” Michalis Sideris says. If all goes as planned, he expects CYPET to face a set of enviable choices: becoming an acquisition target, pursuing an IPO or raising additional capital to fuel further expansion. His father chimes in with quiet conviction, “Our business model is straightforward – manufacturing and selling machinery through our sales managers and agents across different countries, promoting ourselves at exhibitions and in trade magazines. It has served us well for 10 years now and we intend to stick with it. Thanks to our experience in selling PET processing machines, we now have a great opportunity to multiply sales by addressing new market segments of the same industry. We see tremendous growth potential."
This interview first appeared in the December edition of GOLD magazine. Click here to view it.