The choice to pursue alternative routes in response to US tariffs: The operational impact
Stavros Angelidis 08:43 - 07 April 2025
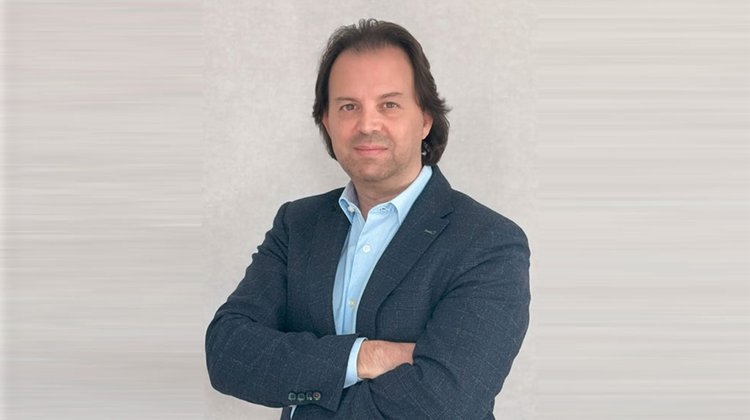
As businesses across various sectors contemplate strategies to navigate the impact of impending US tariffs, a critical decision point arises: Should they pursue alternative routes?
This article aims to explain the daily changes companies should expect when considering or making those changes.
Beyond the widely discussed strategic implications of supply chain restructuring, we explore the subtle yet significant operational challenges that will extend throughout daily business activities.
The potential operational issues discussed herein can affect any business, though the specific impact will vary depending on the type of business, the products involved, and their market positioning.
To this end, this article offers actionable insights for decision-makers weighing the operational realities of shifting away from US-centric supply chains, providing a glimpse into the operational adjustments required for this transition.
The Ripple Effect on Production Scheduling
For companies exploring or implementing shifts away from US sourcing, integrating new suppliers and adapting production models will likely require adjustments to existing scheduling. While companies with agile systems may adapt more readily, others can anticipate potential coordination challenges with unfamiliar vendors, varying lead times, and possible differences in material specifications.
Consequently, companies may need to make more frequent adjustments to production plans and anticipate increased communication. It's important to recognize that supply chains often experience fluctuations, even without tariff changes, and this transition will introduce additional variables.
Therefore, companies should plan for potential increases in rescheduling time and a degree of unpredictability in production output as they navigate these new relationships and processes.
Quality Control and Material Substitution
For companies transitioning away from US sourcing, quality control will require adjustments to maintain consistent standards. As new materials and suppliers are introduced, companies can expect an increase in inspection frequency and detail. Staff may need additional training to effectively inspect these new materials and identify any potential defects. Companies should review and adjust their quality assurance protocols to minimize risks associated with the transition, as any compromise in quality could lead to customer dissatisfaction and reputational damage.
Operations managers will need to closely monitor quality during this period, ensuring that standards are maintained. Companies may also need to update their Standard Operating Procedures (SOPs) to reflect the changes in materials and inspection requirements, which could involve revisions to documentation and additional staff training.
Financial Forecasting and Daily Budget Management
The anticipated financial volatility associated with transitioning away from US sourcing, coupled with the operational adjustments necessary for quality control and material substitution, will introduce some uncertainty into daily financial operations.
Financial teams will find themselves grappling with the challenge of maintaining accurate budgets and forecasts in a rapidly evolving landscape. The increased frequency and detail of material inspections, potential defect rates during transition, and the need to refine SOPs all contribute to rising operational costs.
Daily budget reviews will become more frequent, and less certain, necessitating more detailed financial reports with real-time cost tracking. While larger firms may have robust systems for this, smaller firms may struggle with the resources needed for such detailed, real-time tracking. Decisions regarding daily expenditures and project allocations will require frequent adjustments and careful analysis, considering the increased operational costs tied to maintaining quality standards.
The ability to react quickly to changes in both material costs and operational overhead will be paramount, requiring financial teams to constantly monitor and adapt their strategies.
Product Development and Reactive Redesign
The imposition of US tariffs will trigger reactive product redesigns across a spectrum of businesses. For manufacturing companies reliant on imported components, this translates to urgent engineering adjustments. Distributors and retailers may need to make some packaging changes, but the impact is less dramatic. Regardless of sector, daily engineering workflows and project timelines may be significantly impacted, particularly for manufacturers with tightly integrated global supply chains.
Engineers, accustomed to structured development cycles, may find themselves diverted to address compatibility issues, packaging alterations, or compliance with new regulations.
This can lead to an increase in urgent meetings, rushed prototyping, and immediate adjustments to existing specifications. The daily operational reality will shift from planned improvements to a state of heightened responsiveness, as teams adapt to the new material or regulatory landscape.
Project deadlines will become increasingly fluid, and resource allocation will become more challenging.
Internal Communication and Information Flow
For companies considering a shift away from US sourcing, the potential for swift and multifaceted changes triggered by US tariffs will present communication challenges across all departments and business types.
Manufacturing, distribution, retail, and logistics companies will all grapple with the need to disseminate rapidly evolving operational procedures, material specifications, and regulatory updates. This will necessitate increased communication efforts, requiring more time and resources for information sharing.
Daily operations will be affected by the need for frequent, often impromptu, meetings to address emerging issues and clarify new protocols.
The daily challenge will be to maintain a consistent and accurate flow of operational information, requiring investment in communication tools, clear channels, and a culture of transparency. Especially for companies lacking the right tools, the challenges of tool adoption and implementation time are critical considerations, as these can add to the overall disruption.
However, the implementation of a communication tool (or better a workflow management system) can help avoid delays in communication that lead to operational delays and increased risk of errors.
Making the Decision
For companies contemplating a shift away from US-centric supply chains, the decision extends beyond immediate cost savings and logistical adjustments.
A thorough evaluation of the long-term implications is essential, acknowledging that the operational challenges outlined herein are not permanent but rather a transitional phase. However, this transition can take time. The duration of this phase will depend on the speed of adaptation and the experience and collaboration of all stakeholders across the supply chain.
Companies must also weigh the potential for further political shifts, recognizing that election cycles and changing trade agreements can impact timelines. It is important to note that the urgency of this transition could shift with changes in administrations and trade policies. Repeatedly altering operational processes necessitates investment of time and resources, diverting attention from previously seamless operations.
A meticulous assessment of how alternative sourcing or production models might affect the product performance and quality for the end consumer, and subsequently, the company's brand reputation, is also crucial. A financial analysis, comparing the short-term costs of transition with the potential long-term benefits of avoiding US tariffs, is also critical.
Furthermore, companies must consider the feasibility of such a shift. Some industries or products may be inherently reliant on US-sourced components or technologies, leaving them with limited alternatives.
Regulatory constraints, intellectual property rights, or specialized manufacturing processes may further restrict the ability to make such a change. Therefore, the decision to pursue an alternative route requires a comprehensive, multi-faceted analysis, weighing operational, financial, brand, regulatory, political, and end-consumer considerations, while acknowledging the time-intensive nature of the necessary adaptations. Above all, successful adaptation hinges on robust change management. Companies must prioritize clear communication, employee engagement, and flexible process adjustments to minimize disruption and ensure a smooth transition.
In essence, the choice to pursue alternative options in response to US tariffs is a strategic balancing act, demanding a careful consideration of immediate impacts against long-term operational resilience. In today's unpredictable global trade environment, understanding the operational realities of such shifts is paramount.
As circumstances evolve rapidly, companies must be prepared to make further adjustments, emphasizing the ongoing importance of operational considerations in strategic decision-making.
*Stavros Angelidis provides operations consulting & advisory services www.stavrosangelidis.com